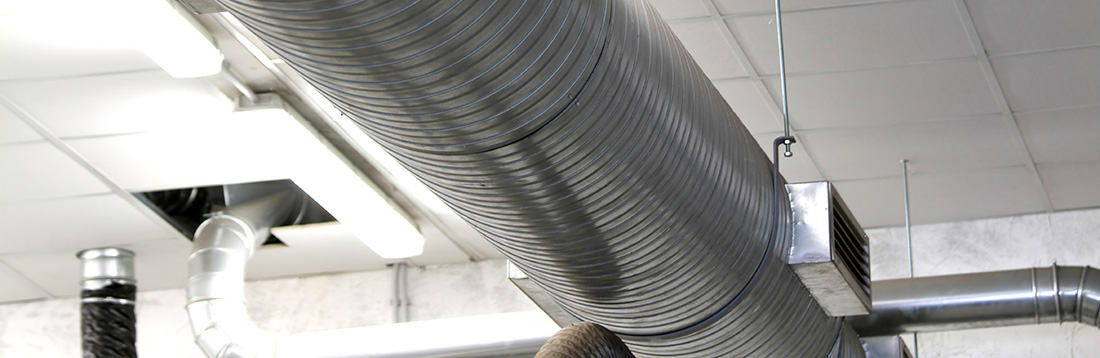
Deciding whether to repair or replace equipment in a commercial HVAC system is something that every facility faces. It would be great if there was some kind of magic formula that would tell managers the perfect time to upgrade, but that’s simply not how it is. Every case is different, and the repair vs. replace decision has to be made strategically. Here are some things to take into consideration when you’re trying to make the right decision for your company.
Cost of Repair Vs. Cost of Replacement
Many people use the rule that if the equipment repair costs will be more than 50-60% of the replacement costs, it may be time to go ahead and replace the equipment. Consider carefully the differences in cost between your two options to see which one is more feasible for your budget. FacilitiesNet states that “optimum service life occurs when cumulative maintenance labor and material costs equal a pump’s replacement cost.”
Potential Energy Savings
Some people are of the mind the repair is always an option. While it’s true that a properly maintained system can be repaired indefinitely (assuming the parts are readily available), at a certain point it may be time to look at the potential energy savings of newer, more efficient systems. Conduct a performance assessment to see whether there are some potential savings on your utility bill you may be overlooking.
Life Expectancy of the Equipment
If your HVAC equipment is over 15 or 20 years old (or beyond its three-quarters life expectancy), you may want to start considering an upgrade. Again, this all comes down to choice in the end as there is no hard and fast rule about equipment life expectancy. An impeccably maintained piece of equipment can function just fine for a long time without needing to be replaced.
Company Policy
This is a big factor is the decision of repair vs. replace for commercial HVAC equipment. Some policies state that repair must always be the first choice when possible. Yearly budgeting can also be a factor. A full system rebuild may not be financially viable for several years, but could be considered for long-term planning. That would mean that the decision automatically defaults to repair.
In-House Maintenance Capabilities
If it’s costing your in-house maintenance team more time to repair equipment (reactive maintenance) than it is to maintain it (preventive maintenance), it may be time for a system upgrade. Also consider how often you’re deferring maintenance—you could be at risk for an HVAC emergency if you put off needed repairs for too long.
There is no general rule about when it is time to repair or replace HVAC equipment. Each facility needs to consider many different factors before coming to the conclusion that will work best for them. If you have questions about what will work best for your facility or want to request a professional assessment, contact Avonda today.
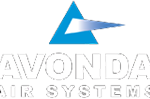
- Choosing an HVAC System When Building a New Home - September 21, 2015
- Mold in HVAC Systems: What You Need to Know - September 17, 2015
- Fall Vermont HVAC Checklist for Commercial Buildings - September 2, 2015
- What You Need to Know About Humidity in Your Vermont Home - August 25, 2015
- Does Your Office Have an Indoor Air Quality Problem? - August 10, 2015
- Stay Cool in Vermont with Ductless Air Conditioning - August 3, 2015
- 4 Things to Consider About Air Conditioning Replacement - July 27, 2015
- 3 Summer Ventilation Tips for Your Vermont Home - July 20, 2015
- Don’t Make These 3 Vermont Air Conditioning Mistakes This Summer - July 13, 2015
- When Should You Call a Vermont HVAC Contractor? - June 22, 2015